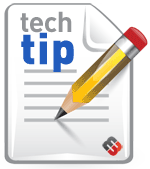
In die attach applications, typically a controlled volume of adhesive is dispensed robotically on the substrate/lead frame and the dies are similarly picked and brought in place. Once attached to the substrate with the adhesive layer in between, this step is then followed by the curing process of the adhesive, based on the recommendation made by the adhesive manufacturer. Often times, a concern during processing is related to bleed out of the adhesive outside the applied areas. While the selection of the type of adhesive is somewhat important while considering bleed out, it is more important to recognize the processing steps that can be taken to eliminate the bleed out.
Causes for bleed out and processing considerations to keep in mind:
- In certain cases, especially if the dispensing process is not automated, there could be an excess amount of adhesive present on the surface,
- The thickness of the adhesive layer applied has to be such that there is minimal squeeze out while the die is being attached to the substrate.
- Generally, non-flowing/minimal flowing thixotropic pastes that can be dispensed and cured quickly are desired for such applications.
- A faster setting/curing system is generally better to avoid any heat thinning effects.
- Any surface contamination can have an adverse impact, which could lead to bleed out.
- Plasma cleaning and etching can be used to prevent such contamination.
Excess adhesive present on the surface:
Viscosity of the compound selected, and the cure schedule:
Surface contaminants: